Comparing: Teflon Encapsulated O-Rings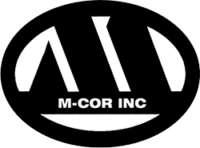
Resellers and the Importance of Country of Origin
Some resellers focus on higher profit margins instead of product quality. They often buy from knock-off manufacturers, ignoring the effects on performance, compliance, and safety. Therefore, always verify the product’s country of origin when choosing Teflon encapsulated O-rings. This step helps confirm that materials and processes follow recognized standards.
Comparing: Teflon encapsulated O-rings is crucial in industries such as chemical processing, pharmaceuticals, aerospace, and semiconductor manufacturing. They provide strong chemical resistance, high-temperature performance, and reliable sealing. However, the market also offers cheaper offshore O-rings that frequently fail to meet strict specifications. Thus, understanding the differences in materials, dimensional accuracy, and potential risks is vital when selecting Teflon encapsulated O-rings.
Material Composition and Manufacturing Process
Offshore manufacturers sometimes use lower-quality or recycled materials to reduce costs. Premium Teflon encapsulated O-rings feature Virgin FEP (fluorinated ethylene propylene) or PFA (perfluoroalkoxy) jackets, while certain offshore products rely on weaker PTFE recycled blends. Consequently, these O-rings can fail in harsh chemicals or high temperatures. Furthermore, their elastomer cores are often generic silicone or EPDM, which can lead to permanent deformation (compression set) that reduces sealing performance.
In contrast, quality manufacturers typically follow strict material standards. They may use FDA-compliant or USP Class VI materials, and they also employ precise production methods to minimize dimensional variations. In addition, they offer specialized elastomer cores—such as PFAS-free EPDM ( M-Cor formulated elastomer) or premium-grade silicone, FKM/Viton—to extend service life and improve chemical resistance.
Dimensional Tolerances and Quality Control
Precise dimensions are essential for effective sealing. Offshore suppliers often neglect robust quality checks, which can result in inconsistent cross-sections and inner diameters. This lack of uniformity may lead to leaks or mechanical failure. Meanwhile, domestic suppliers usually provide thorough documentation for traceability and regulatory compliance. As a result, customers can trust that these O-rings meet established industry criteria.
Common Risks of Low-Quality Teflon Encapsulated O-Rings
-
Chemical Degradation
Weak Teflon jackets are prone to cracks in aggressive chemicals, exposing the elastomer core and speeding up seal failure. -
Abrasion and Scratching
Thinner Teflon layers can scratch easily in abrasive conditions. Even small scratches allow chemicals to attack the core. -
Thermal Limitations
Inferior Teflon may split from the core during repeated heating and cooling, causing premature seal breakdown at lower temperatures. -
Compression Set
Poor-quality elastomer cores can flatten under constant pressure or heat. This deformation prevents proper sealing. -
Dimensional Variability
Inconsistent cross-sections or diameters can create leaks and lead to costly downtime for repairs. -
Lack of Certifications
Offshore products may not carry FDA or NSF approvals, risking contamination and liability in sensitive applications.
Economic and Compliance Considerations
Although offshore O-rings seem less expensive at first, frequent replacements, production stoppages, and equipment damage can quickly raise total costs. Furthermore, industries that require certified products face non-compliance risks if they use uncertified O-rings. In food and pharmaceutical operations, using substandard seals can result in recalls and legal issues, which far exceed any initial savings.
Solutions for Reliable Sealing
-
Demand Material Transparency
Ask for certification and test data. Reputable suppliers will share details on material composition and purity. -
Specify Exact Standards
Follow recognized guidelines for dimensions and set strict tolerances. Doing so helps ensure a proper seal gland fit. -
Choose Specialized Compounds
Use premium elastomer cores, such as PFAS-free EPDM or high-purity silicone, for better durability in aggressive chemicals or high temperatures. -
Assess Regulatory Compliance
Verify that O-rings meet FDA, USP Class VI, or NSF standards if required. Also check that the supplier maintains strong quality control systems. -
Perform Lifecycle Cost Analysis
Look beyond the unit price. Calculate overall costs, including maintenance and downtime, to find the most cost-effective long-term option.
Conclusion
When choosing Teflon encapsulated O-rings, it is important to evaluate material composition, dimensional precision, and quality control. Low-priced offshore products may appear attractive, yet they often lack chemical resistance, thermal reliability, and adequate lifespan. Ultimately, selecting high-quality materials and tested manufacturing practices lowers total costs over time and provides confidence in demanding applications.